According to the Load Restraint Guide, several factors come into play when determining the capacity of tie-down lashings. Let’s delve into these key considerations to better understand how to secure your loads effectively.
Friction and Pre-tension:
The amount of friction between the load and the deck surfaces significantly impacts the weight each lashing can restrain. Simply put, greater friction equals more weight restraint. Additionally, the pre-tension applied to a lashing also affects its capacity. The higher the pre-tension, the more weight the lashing can restrain. Therefore, it’s crucial to ensure proper friction and tension are achieved during the lashing process to maximise load security.
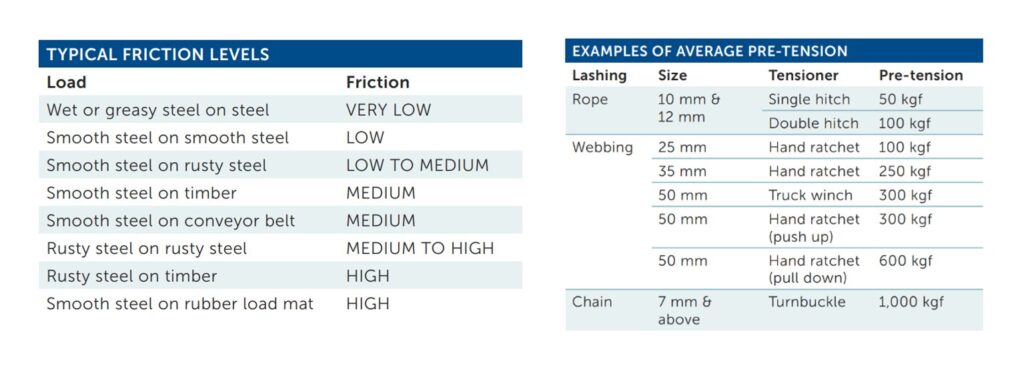
Angle Effect:
Tie-down lashings are most effective when they are vertical and tight. Any angle away from the load reduces the clamping force, known as the angle effect. For instance, a lashing at a 90° angle provides more clamping force than multiple lashings at a 15° angle. Understanding this principle helps determine the number and positioning of lashings required for optimal load restraint.
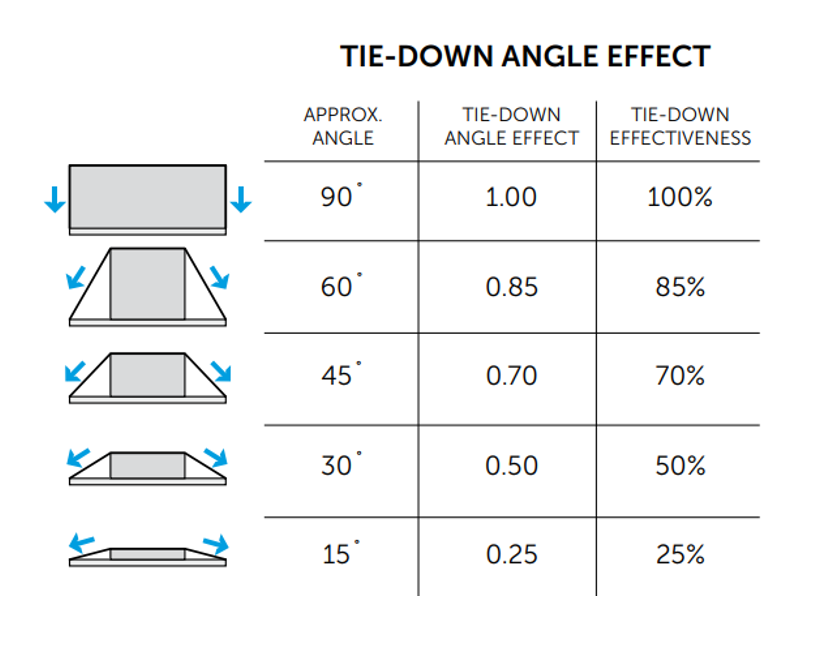
Blocking and Equipment:
Whether a load is blocked using rated equipment also influences the number of lashings needed. When properly blocked, some of the required restraint can be achieved by the equipment itself. This consideration can reduce the number of lashings required, provided the blocking equipment meets safety standards and is appropriately utilized.
Determining Lashing Requirements:
To calculate the number of lashings needed for a load, divide the total weight of the load by the weight each lashing can restrain, then round up to the next whole number. It’s essential to note that the pre-tension in a lashing does not directly correlate to the weight it can restrain, emphasizing the importance of proper calculations and adherence to safety guidelines.
Direct Lashings:
Direct lashings involve using webbing straps, chains, or twist locks to attach a load directly onto a vehicle. They are particularly suitable for loads with little or no friction between the load and the loading deck, such as slippery loads or loads on wheels. The required strength of a direct lashing depends on factors like the load’s weight, the number of lashings, and their direction. Manufacturers typically mark the lashing capacity or rating on the equipment, providing clear guidelines for safe usage.
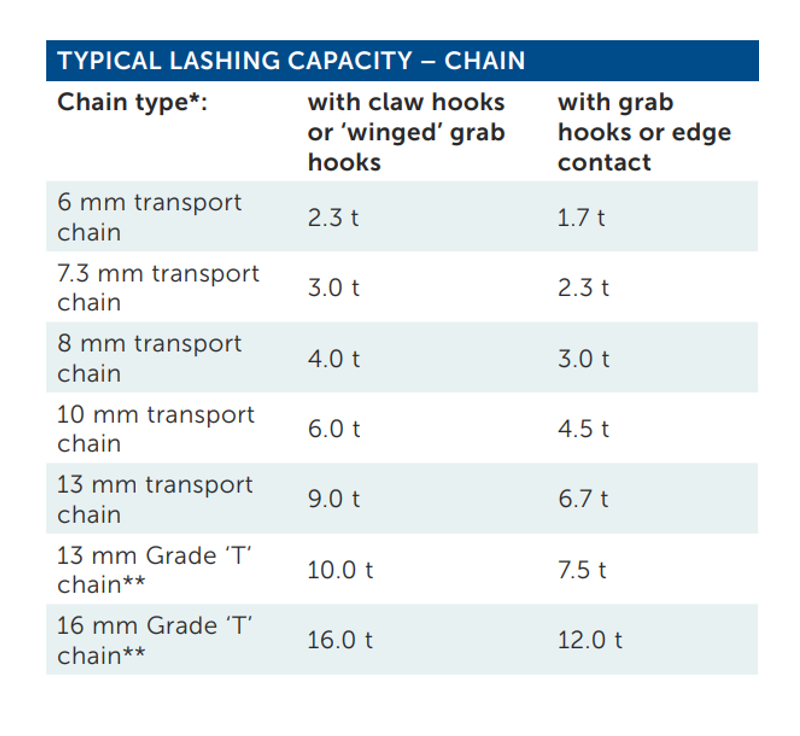
By considering factors such as friction, pre-tension, angle effect, blocking, and equipment, you can determine the appropriate number and positioning of lashings needed to secure your load effectively. Whether using direct lashings or other methods, prioritising safety and adherence to guidelines is key to successful load transportation.